Abstract
picosecond laser glass cutting has emerged as a cutting-edge technology revolutionizing the precision glass cutting industry. The increasing demand for laser glass cutting for a variety of industries from displays through cellular devices to structural glass is pushing an expansion in the picosecond laser machine builders business, due to the advantages of using ultra-short pulsed lasers for smooth sidewalls and high throughput. In this short article we delve into the physics of picosecond laser glass cutting, highlighting the need for focal beam shaping to achieve optimal results. By employing diffractive axicons or improved modified Bessel solutions such as DeepCleave , picosecond laser machine integrators can overcome limitations and enhance cutting throughput and quality.
Background: Picosecond Laser Glass Cutting Mechanism and requirements
The demand for laser glass cutting has grown exponentially across disparate industries, from hard and thin glass cutting for cellular phones and displays to shipbuilding and structural glass cutting, where thicker glass components are required for enhanced durability. Ultra-short pulsed lasers have become the technology of choice for this purpose, offering precise cuts with smooth sidewalls and high throughput, aligning with the growing need for intricate glass components.
Picosecond laser glass cutting relies on ultra-short pulsed lasers, typically at ~1um wavelength creating plasma filamentation within the glass, leading to the evolution of internal stress. This stress can induce cleaving of the laser processed line with smooth, clean seam, by the application of slight thermal or mechanical stress. Cleaving with picosecond laser side effect includes micro-cracking and void formation and can be minimized by correct choice of processing parameters, including pulse frequency, pulse energy and cutting speed.
The non-linear absorption characteristics of the picosecond laser cutting process confine the effected region to a narrow diameter, typically 1-5um, while the depth of focus must span the entire glass thickness, which can range from 0.2mm to 20mm, depending on the application. Gaussian beams cannot be focused to a tight enough spot while having a large depth of focus, due to the inherent limitations of the Rayleigh range, necessitating beam shaping to achieve Bessel-like beams that have this extended focus range.
The Need for Focal Beam Shaping in Picosecond Laser Glass Cutting
Methods such as axicon-generated Bessel-like beams and multifocal DOEs have been explored for focal beam shaping. However, standard refractive axicon often are less suitable Bessel beam generation in glass cutting applications. This is because they have non active regions near the axicon tip, high surface quality requirements, and are challenging to grind with accurate low head angle required for some glass thicknesses. Diffractive axicons emerge as a solution, as they have no inactive tip zone, have near perfect wave front flatness and absolute angular accuracy.
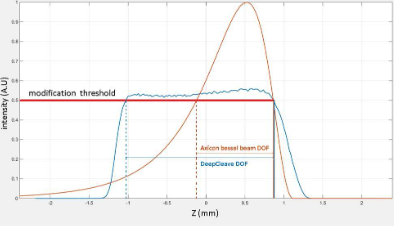
Improved Performance Focal Shaping by Modified Bessel-like Beams:
One limitation of normal Bessel-like beams is their non-flat intensity profile along the focal axis, leading to wasted energy below and above the glass cutting threshold . Modified Bessel beam solutions such as DeepCleave provide a flat top intensity profile along the focal depth, optimizing cutting efficiency and throughput with the same picosecond energy thus providing a significant improvement in performance.
Experimental demonstration of the benefits beam shaping offer to picosecond laser glass cutting
Holo/Or has cooperated with many different integrators and laser manufacturers in various glass cutting projects. One of our cooperative projects was with Fluence technology, a picosecond laser producer, in their application lab demonstration of glass cutting. Results show good quality cuts at high rate in fused silica and soda lime glasses- you can read the full report here
Summary
The demand for advanced laser glass cutting solutions is on the rise, driven by various applications and the need for thicker glass components. Ultra-short pulsed lasers offer numerous advantages for laser glass cutting, but proper beam shaping is crucial to achieve optimal cutting results. Diffractive axicons and modified Bessel-like beam modules provide the solution for enhanced focal beam shaping, overcoming previous limitations and unlocking new possibilities in the glass cutting industry.
TL;DR:
How do ultrashort pulsed lasers contribute to precise glass cutting?
Ultrashort pulsed lasers generate plasma filamentation in the glass, creating internal stress and allowing for precise high throughput cutting with smooth side walls.
Why is beam shaping needed in picosecond laser glass cutting?
the nonlinear absorption process used in ultra short laser cutting of glass requires high power densities, thus the laser must be focused to a tight spot. For standard gaussian beams, this means the depth of focus is limited by the Rayleigh range and cannot cover the entire glass thickness. Diffractive beam shaping is needed to extend the focal depth in the glass, enabling one-pass cutting.
Why are diffractive axicons better for glass cutting compared to regular axicons?
Regular Axicons have dead regions near the axicon tip and are challenging to produce with the optical quality needed for Bessel beam generation, especially for low head angle axicons required for many glass thicknesses. Diffractive axicons eliminate dead regions, have better surface quality since they are flat windows, and have absolute angular accuracy even at low head angles.
How do modified Bessel-like beams improve cutting efficiency?
Modified Bessel beams generated by such DeepCleave create a flat top profile along the focus axis, unlike the non-flat profile of axicon generated Bessel like beams. This flat top profile optimizes cutting efficiency by reducing wasted energy below the glass cutting threshold, resulting in higher speed cutting / thicker glass cutting at the same speed , with the same laser energy.