Introduction: Beam splitter optics and battery laser texturing
The electro mobility revolution is constantly pushing producers to improve battery performance. A process of interest is laser texturing of electrode surfaces, which has shown promise in increasing the discharge/ charge speed, reducing degradation, and improving efficiency in car Li-Ion batteries.
To be feasible in industrial scale production, laser texturing processes must deliver high throughput, at least 1m2/min. Such high rates require sophisticated beam handling to distribute the laser energy over large areas in a distinct pattern. To achieve this, beam splitter optics, and specifically diffractive beam splitters, are often employed in the laser texturing process. In this article we will explore the technical aspects of how diffractive beam splitters work and their impact on large area texturing.
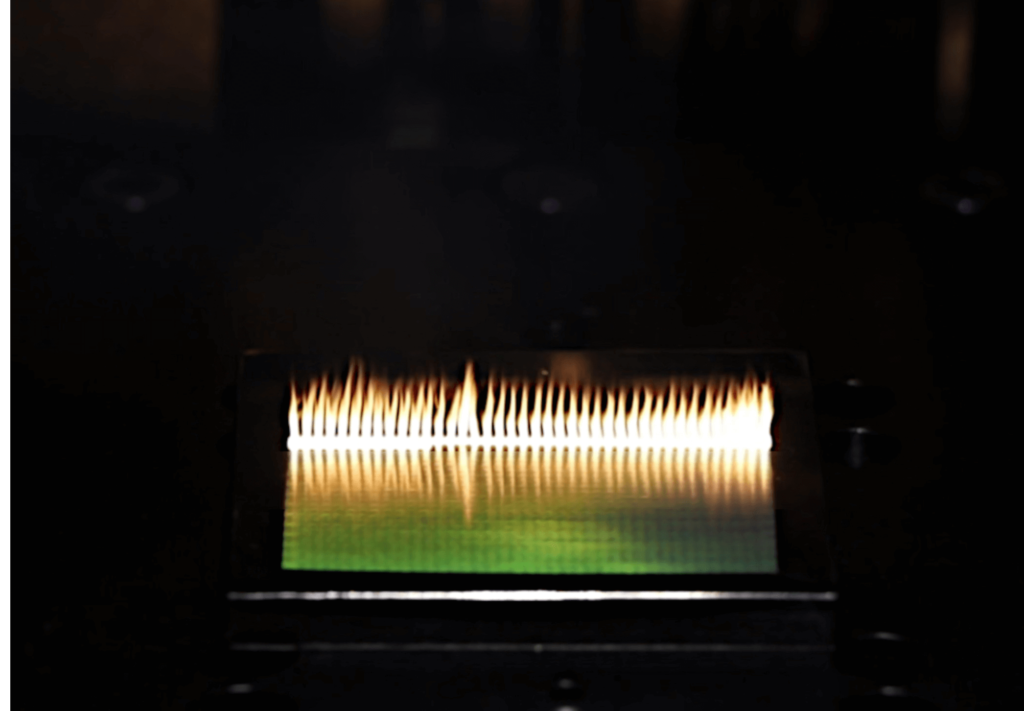
Understanding Diffractive Beam Splitters
Diffractive beam splitters are optical grating-like transmissive elements that employ diffraction to split an incoming laser beam into multiple discrete spots. Unlike simple gratings which send the light into two main orders, diffractive beam splitter optics can create any array of spots, including large 2D arrays of spots with equal separations and uniform intensity. They do this by having periodic complex micro- features on their surface that serve to create a controlled delay of the laser light going through the DOE. This delay creates a diffraction profile that can be tailored by the design of the beam splitter elements.
The number, position, and intensity of the laser spots generated can be precisely determined, allowing for high accuracy texturing.
Large Area Texturing- why use beam splitter optics?
Large area laser texturing is crucial for battery electrode manufacturing to achieve uniform and controlled texture across a significant surface. The main challenge in battery electrode laser texturing is the spreading of laser power over the surface in a structured way. For this purpose, diffractive beam splitters are invaluable, as enable the laser to be split in a controlled manner corresponding to the desired surface structure pitch and can split to as many structuring spots as the laser power allows.
Scanning Schemes for Achieving Target Throughput
To achieve the target throughput rate of 1 square meter per hour in battery electrode texturing, various scanning schemes are employed. These schemes involve the movement of the laser beam and/or the workpiece to cover the desired area efficiently. Common scanning schemes include:
- Pure Galvo scanning: Galvanometer scanners are used to steer the laser beam across the workpiece, coupled with a F-theta focus lens. They offer high-speed and precise control, making them suitable for applications that require rapid texturing. Often in such a scheme, a 2D beam splitter is placed before the F-theta an creates a rectangle of texturing spots, with the galvo stitching the processing area. This method is fast but limited to large feature surface structures (typically 10um or more for IR lasers ) due to the available NA of F-theta scan lenses.
- Fast axis Stage scanning: In stage scanning, the workpiece itself is moved relative to a stationary laser beam. In this method, 1D beam splitters are often used to create a line of spots, that is then rapidly scanned using fast axis movement, resulting in a textured strip. This strip is then stitched by movement in the other axis, and another strip is scanned. This method is fast and can reach a high NA (small features in the textured surface) but is generally not very flexible- it is best suited to large areas with full coverage, less of the case when considering battery electrodes.
- Galvo+Stage scanning: A combination of galvo and stage scanning offers a compromise between speed and flexibility. The galvanometer scanners control the laser beam’s fast movements, while the workpiece’s stage provides slower but broader movements. In this regime a square pattern of spots is often used, generated by diffractive beam splitter optics. Often, each system requires a different, custom beam splitter, tailored for the specific processed electrode geometry. You can see Holo/Or’s beam splitter performance for this type of in our DLIte page.
Requirements and constraints of using beam splitter elements for laser texturing
Beam splitters are generally robust element that are not sensitive to tolerances such as positioning, small tilts, or beam size. However, using a beam splitter in laser texturing applications does require several considerations:
- Minimum beam size- The system apertures must support the angles generated by the beam splitter without clipping
- Field correction- The focus optics used must compensate for the field distortion at higher splitting angles. This is mostly relevant when working with large fields such as in fast axis scanning.
Conclusion
Diffractive beam splitters play a crucial role in battery electrode laser texturing, enabling large area texturing with enhanced efficiency and precision. Their ability to generate multiple laser spots makes them ideal for achieving uniform electrode texture. To meet the target throughput rate of 1 square meter per hour, various scanning schemes, such as galvo, fast axis stage, and galvo+stage scanning, are utilized.
These scanning methods ensure that the texturing process is not only technically sound but also practical for industrial applications. As technology continues to advance, the integration of diffractive beam splitters and advanced scanning techniques will further optimize the laser texturing process in battery electrode manufacturing.
TL;DR:
How is laser texturing useful for battery electrodes?
Laser Texturing of electrode surfaces has been shown to increase discharge/charge speed, energy efficiency and durability of batteries
What are diffractive beam splitter optics?
Beam splitter optics are diffractive optical elements that split an input beam into an array of spots with equal separations.
How are beam splitter optics used in laser surface texturing?
There are many schemes for laser surface texturing, most using some sort of movement of the beam (by galvo mirror) or the workpiece (by fast axis stage). In all these schemes, the use of diffractive beam splitters enables high throughput texturing over large areas.
what are the requirements for using diffractive beam splitter optics in a texturing system ?
The main requirements are sufficient clear aperture, and the use of field-corrected focus optics (such as F-theta lenses).